To achieve the best quality, use the best Quality Control.
Few if any customers become repeat buyers if your product’s quality is less than what it could or should be.
But one reason why it’s so challenging to achieve optimum quality involves the many variables that can go wrong: variations in raw materials, human error, machine failure, improper use of machines or production methods, failed inspections and more.
To keep from having unhappy customers, you need to set up procedures and methods to control the quality of your products from beginning to end.
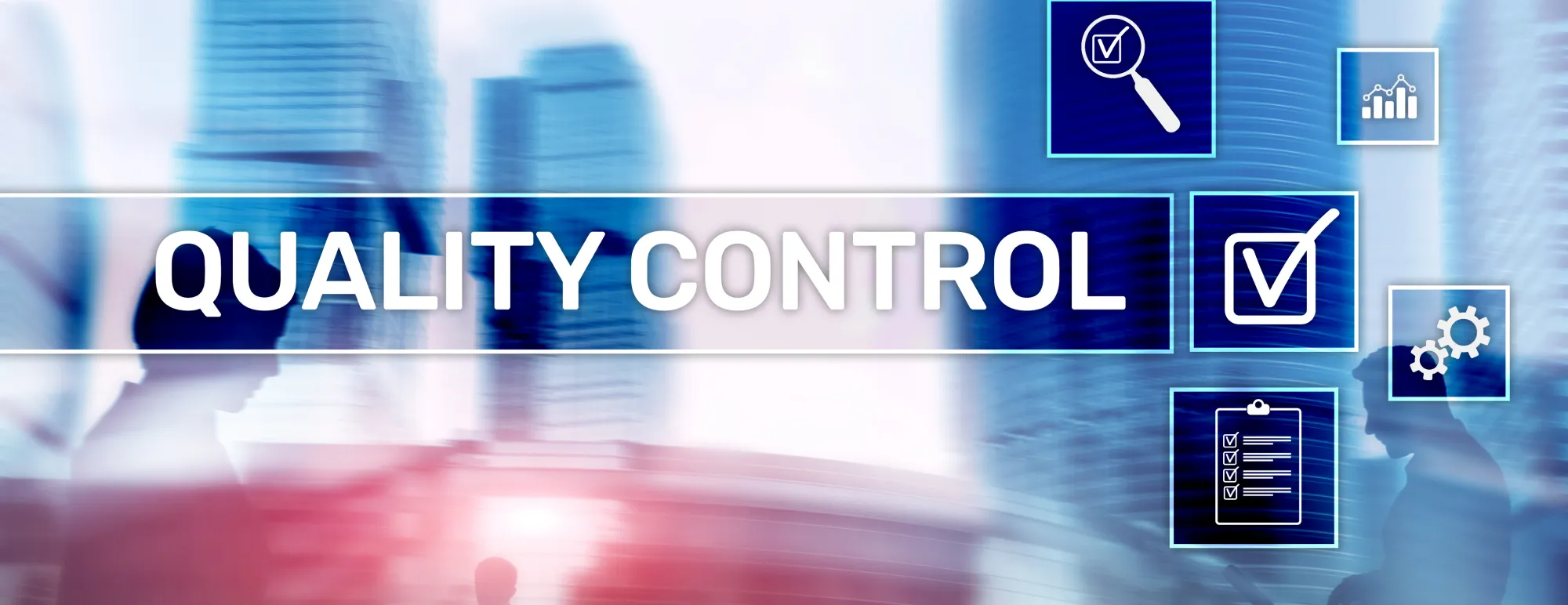
The multiple valuable benefits of strong quality control.
It gives customers confidence and trust in you and your products.
It preempts potential problems from occurring in the first place.
It saves you money in the long run by minimizing product returns.
It enhances your company’s image and reputation in the marketplace as a reputable company.
It serves as a foundation for continuous improvement.
Quality control in general.
The following describes actions that most manufacturers need to take.
Monitor and critically evaluate your current production processes.
Based on those findings, establish new production standards that are exacting yet achievable.
Define what a batch and sample are for your company.
Analyze sample units from the batch and determine their level of quality.
Identify which sample units passed inspection and which did not. Often there will be units that can be reprocessed, but those that can’t be should be rejected. If the number of defective units in a batch is high, you may decide that the entire batch needs to be scrapped.
Analyze discarded units to discover the underlying cause(s) and how they can be corrected, then implement the needed change(s). This may involve changes to the team, staff training, modification of the raw materials or other such actions.
Solutions are not easy but definitely needed.
Here are the key steps to take:
Set up a Production Part Approval Process (PPAP).
This will let you evaluate the components and subsystems you get from each supplier and to institute design specs that ensure better compliance. You can then easily manage changes to products and processes, along with evaluating future suppliers.
Establish a receiving and inspection process.
You’ll be able to not only better coordinate the process of receiving materials but also to have your inspection schedules based on your experience with supplier performance.
Consider a Slip-lot sampling process.
Use it to track and evaluate quality in real time, reduce defects in finished products and make sure inspections are conducted consistently.
Establish Supplier Corrective Action Requests (SCAR).
It will give you a root-cause analysis, corrective planning and risk analysis in order to make readily visible anything that fails to meet specifications.
Manage the Approved Supplier List.
It’s critical to provide real-time measurements of supplier and material performance. The review and approval workflow are designed to deliver transparency and control over the qualification process.
Utilize supplier ratings.
These will give you detailed information on supplier performance, all in one place, so you can quickly see all facets of your supplier relationships.
Broaden your quality management.
Along with your quality team, include everyone who has a relationship with your suppliers.
Make suppliers part of your quality system.
They should be involved in your Quality-management System (QMS) and workflows as accountable members of the process and developers of the solution. When systems are fully integrated, constant communications across systems can be implemented.
Don’t fall behind the times.
If these processes are done manually by humans – which is still often the case – costly errors are just waiting to happen.
That is why you need to employ modern technologies to enhance supply-chain performance instead of trying to upgrade existing systems. In addition to solving quality problems, they enable manufacturers and suppliers to be on the same page and to know what the expectations are.